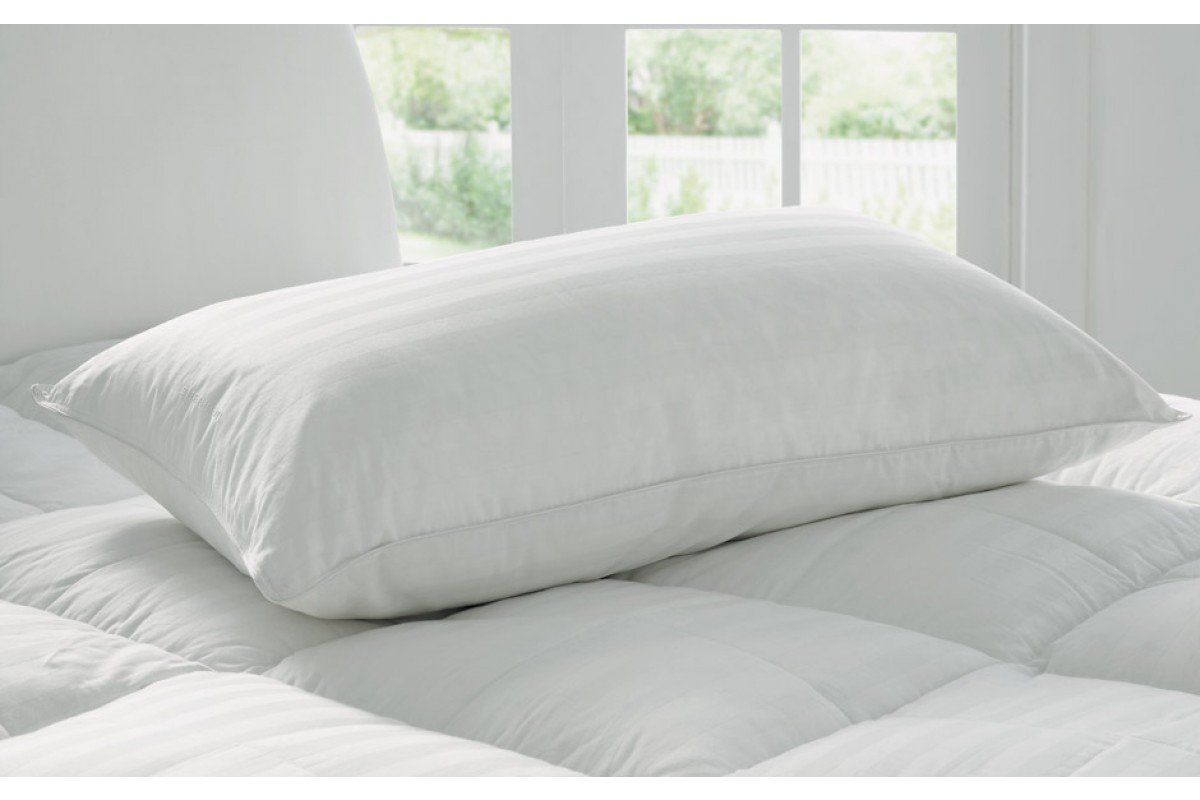
Managing the Pillow Prices in Pakistan due to the ever-changing market trends and client needs and preferences. Continuing with the meanwhile unused objects, pillows can be considered as one of the most important items that people use at home affecting the quality of the sleep and level of comfort. Knowledge of how to approach price management ensures the businesses earn a better profit while meeting consumers’ needs in a satisfactory manner.
Factors Influencing Pillow Prices
Numerous factors determine the Pillow Price in Pakistan. Some of them include the cost of the raw materials used in the production of the pillow, the manufacturing charge, the labor charge, and the market requirements. Some examples could include the following: if a designer finds that expensive fabric from overseas is the best for a piece they are designing, it will add up to their cost, while the local material could prove cheaper.
Description of Some Selected Pillow Brands and Costs
There are different types of pillows, and these come with various prices. Some types of pillows, such as memory foam pillows, are relatively expensive because of their production materials and processes. Polyester or cotton-filled pillows are generally cheaper than water-filled pillows.
Conducting Market Research
Thus, the effective management of pillow prices requires the gathering as well as analysis of market information. This entails practising constant market analysis or implementing the ability to conduct research on the market trends in the present market, customer relations, or competitor tracking.
Trend Analysis on Price of Pillows
Experts in analyzing data can determine the trends in order to forecast the future prices. For example, if there is upsurge in the market for organic pillows then the costs of such products may be high often because their production is small-scale and expensive.
Cost Management Strategies
There are a number of potential methods through which costs related to the making of pillows and prices of pillows can be controlled; One is the purchasing of the material at a cheaper rate. Thus, it becomes manageable and easily possible to minimize the costs of the materials usually by developing relations with the local suppliers or with the bulk purchases.
Efficient Manufacturing Processes
Reducing the of production steps may also reduce the manufacturing costs. By adopting lean manufacturing and purchasing high level machines, productivity can be boosted and wastage minimized.
Pricing Strategies
Taking a cue from the competitors entails pricing strategies that are determined from prices charged by competitors. It can also assist in attracting the consumer with price sensitivity strategies.
Value-Based Pricing
Value-based pricing focuses on the perceived value of the product to the customer. For high-quality or unique pillows, setting a higher price can be justified if the customers see added value.
Dynamic Pricing
Dynamic pricing involves adjusting prices based on market demand and supply conditions. This flexible approach can maximize profits during peak demand periods.
Supply Chain Management
An optimized supply chain can significantly reduce costs. Efficient logistics and inventory management ensure that materials and products are where they need to be when they need to be, minimizing delays and extra costs.
Reducing Logistics Costs
Negotiating better rates with logistics providers and using technology to track and optimize shipping routes can help reduce logistics costs.
Maintaining Quality without Increasing Costs
Maintaining high quality is essential for customer satisfaction. Implementing strict quality control measures ensures that products meet standards without necessarily increasing costs.
Importance of Customer Satisfaction
Satisfied customers are more likely to make repeat purchases and recommend the product to others, which can enhance sales without the need for significant price adjustments.
Marketing and Promotion
Effective marketing can drive sales and justify higher prices. Highlighting unique selling points, such as comfort or durability, can attract customers willing to pay more.
Technological Integration
Technology can play a crucial role in managing costs. Inventory management systems, for example, can prevent overstocking or stockouts, while automated manufacturing processes can reduce labor costs.
Managing Cash Flow
Managing cash flow ensures the business can cover costs while investing in growth opportunities. Regularly reviewing financial statements can help monitor financial health.