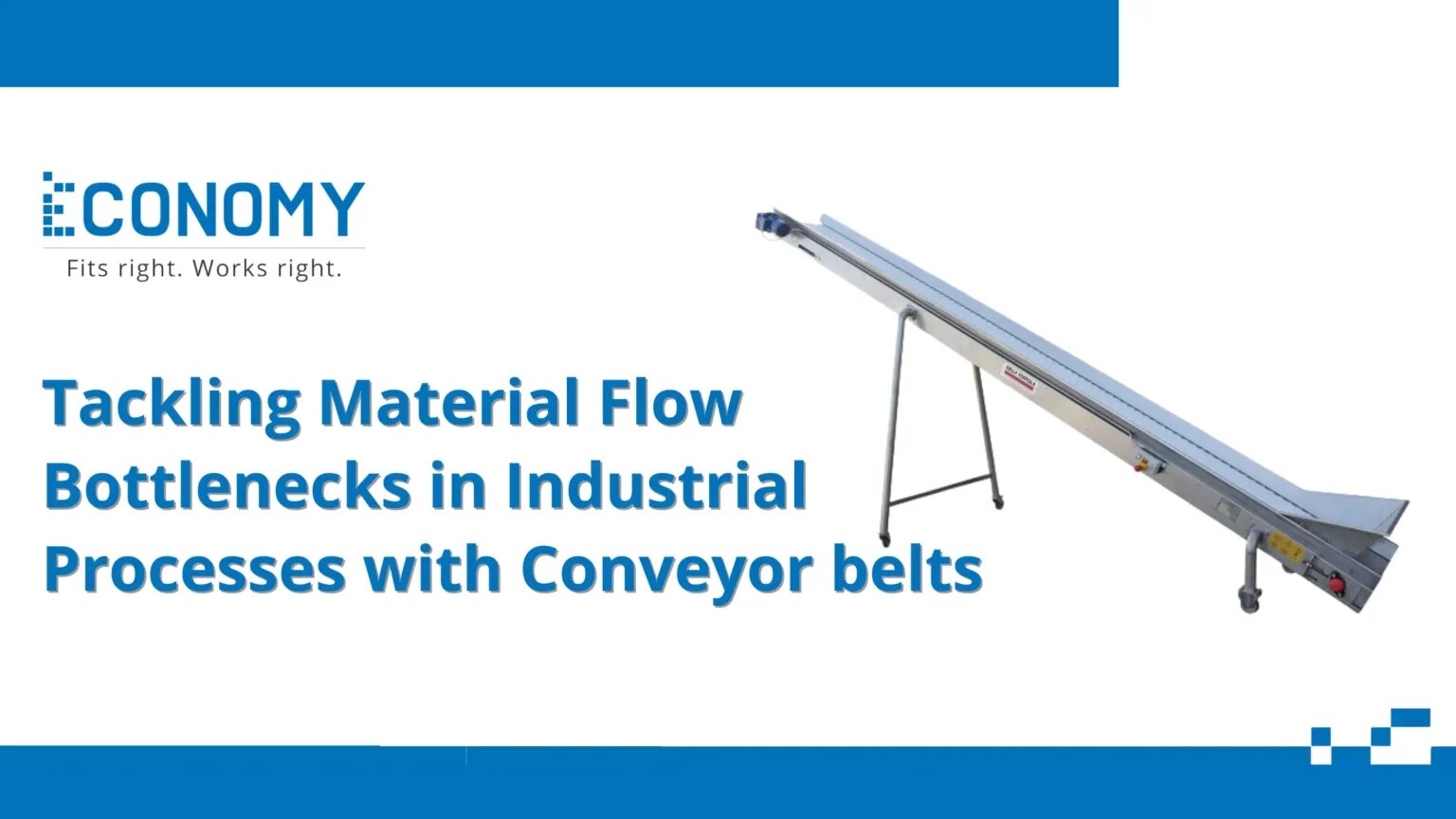
Understanding Material Flow Bottlenecks
Understanding material flow bottlenecks is crucial for optimizing industrial processes and ensuring smooth operations. A bottleneck occurs when the capacity of an element in a production line is less than the demand placed upon it, causing delays and inefficiencies. Identifying these choke points involves a thorough analysis of the entire material flow, from raw materials entering the facility to finished products ready for shipment.
In many industrial environments, conveyor belts are integral to material movement. However, if not properly managed, they can become significant sources of bottlenecks. For example, insufficient belt speed or inadequate width can limit throughput, while misalignment or mechanical failures can halt production entirely. Additionally, uneven distribution of materials on the conveyor belt can lead to congestion and slow down subsequent stages of processing.
To effectively address these issues, it’s essential to employ both qualitative assessments and quantitative tools such as flow simulations and real-time monitoring systems. These tools help pinpoint where delays are occurring and why they happen. By understanding these dynamics, plant managers can implement targeted solutions such as upgrading conveyor belt specifications or redistributing loads more evenly across the system.
The Role Of Conveyor Belts In Industrial Processes
Conveyor belts are integral to modern industrial processes, serving as the veins through which materials flow seamlessly from one stage of production to the next. These mechanical systems are designed to transport a variety of goods, ranging from raw materials to finished products, across different sections of a manufacturing plant with minimal human intervention. The role of conveyor belts in industrial settings cannot be overstated; they enhance operational efficiency by ensuring a continuous and consistent movement of items, thereby reducing delays and minimizing manual handling.
A well-designed conveyor belt system can significantly improve productivity by streamlining workflows and optimizing the use of space within a facility. By automating the transportation process, companies can achieve higher throughput rates and better synchronize their operations. Additionally, conveyor belts contribute to workplace safety by mitigating the risks associated with manual lifting and carrying tasks.
Identifying Common Causes Of Bottlenecks
Identifying common causes of bottlenecks in material flow is essential for optimizing industrial processes involving conveyor belts. One prevalent issue is the inconsistency in the supply of raw materials, which can lead to imbalanced loads on the conveyor system. This irregularity often causes delays and interruptions, hampering the efficiency of downstream operations. Another significant factor is the mechanical limitations of conveyor belts themselves.
Wear and tear, inadequate maintenance, and suboptimal design can reduce their effectiveness and throughput capacity.
Furthermore, human error plays a considerable role in creating bottlenecks. Mismanagement or poor coordination among workers responsible for loading and unloading can result in uneven material distribution along the conveyor belt. Additionally, varying processing speeds at different stages of production can cause backlogs if not properly synchronized.
Assessing Conveyor Belt Efficiency And Capacity
Assessing the efficiency and capacity of conveyor belts is essential for identifying and mitigating material flow bottlenecks in industrial processes. An efficient conveyor system ensures that materials are transported smoothly, minimizing downtime and maximizing throughput. The first step in this assessment involves analyzing the current operational parameters, such as belt speed, load capacity, and cycle times. By comparing these metrics against production demands, it becomes possible to pinpoint discrepancies that may be causing inefficiencies.
Moreover, evaluating the physical condition of the conveyor belts is crucial. Wear and tear can significantly impact performance; thus, regular inspections for signs of degradation like fraying edges or misaligned rollers are necessary. Advanced diagnostic tools can also be employed to monitor real-time performance data, providing insights into potential issues before they escalate into major problems.
Technological Innovations In Conveyor Systems
The advent of technological innovations in conveyor systems has significantly transformed the landscape of industrial processes, particularly in addressing material flow bottlenecks. Modern conveyor belts are no longer simple mechanical systems; they have evolved into sophisticated, automated solutions that integrate seamlessly with advanced manufacturing operations.
One key innovation is the incorporation of smart sensors and IoT (Internet of Things) technology. These sensors provide real-time data on belt performance, load distribution, and potential obstructions, enabling predictive maintenance and reducing downtime. By anticipating issues before they escalate into critical failures, these intelligent systems ensure a smoother material flow and enhance overall process efficiency.
Another pivotal development is the use of modular conveyor designs. These modular systems offer unparalleled flexibility, allowing for quick reconfiguration to meet changing production demands or to bypass areas experiencing congestion. Additionally, advances in materials science have led to the creation of more durable and efficient belt materials that reduce wear and energy consumption.
Strategies For Optimizing Conveyor Belt Performance
Optimizing conveyor belts performance to tackle material flow bottlenecks in industrial processes requires a multifaceted approach that addresses both the mechanical and operational aspects of the system. Firstly, ensuring that the design and installation of conveyor belts are tailored to the specific needs of the process can significantly mitigate inefficiencies. This involves selecting appropriate belt types, materials, and configurations that align with the nature of the materials being transported, as well as their required speed and volume.
Regular maintenance is paramount to sustaining optimal performance. Implementing a rigorous inspection schedule allows for early detection of wear and tear, misalignments, or other potential issues that could lead to downtime or reduced efficiency. Advanced monitoring systems can be employed to provide real-time data on belt conditions and performance metrics, enabling proactive interventions.
Case Studies: Successful Implementation Of Conveyor Solutions
In examining the successful implementation of conveyor solutions to address material flow bottlenecks, one case stands out from a manufacturing plant specializing in automotive parts. The plant faced significant delays due to manual handling and inefficient material movement between different production stages. By integrating a network of automated conveyor belts, the facility transformed its workflow.
The conveyors were strategically placed to connect critical points within the production line, ensuring seamless transitions of materials. Advanced sensors and control systems were incorporated to monitor load and pace, automatically adjusting belt speeds to prevent congestion. This smart system not only streamlined operations but also enhanced safety by reducing human error associated with manual handling.
In another instance, a large-scale food processing company tackled similar challenges by adopting modular conveyor belts designed for quick reconfiguration. This flexibility allowed them to adapt swiftly to changes in product types and volumes, minimizing downtime during shifts in production focus.