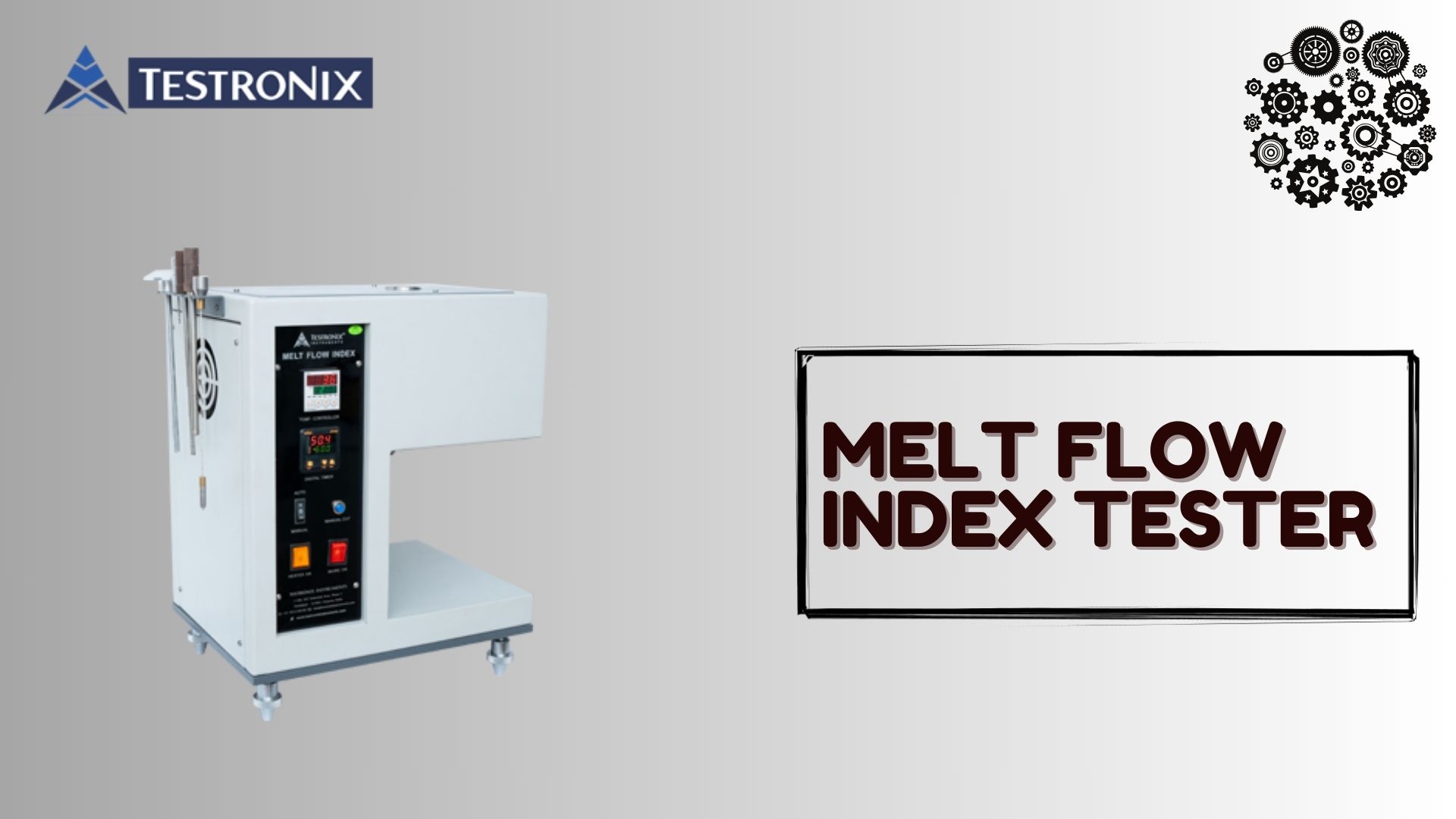
The melt flow index tester is actually a very important tool for the plastics and polymer industry. It measures the flow rate of molten plastic under specific conditions offering you important insights into material properties and processing behavior. Choosing the right melt index tester plays a very important role in obtaining reliable data and ensuring efficient quality control. In this guide you can learn everything about the key factors to consider when choosing MFI tester.
Essential features for accurate measurements
· Perfect temperature control is really important for consistent and accurate results. When evaluating the tester, you need to look for temperature control features like platinum resistant temperature detectors. It is mainly your best bet because of its high accuracy and reliability. The sensors ensure that the temperature readings are perfect leading to more consistent MI measurements. A well-designed heating system ensures even heat distribution within your barrel avoiding temperature variations that can impact the flow rate of your molten plastic you need to look for testers with multi zone heating systems and maintain a consistent temperature throughout the testing.
· You need to choose a tester that accommodates your range of weights to measure different melt flow rates for the flexibility makes it very easy to test different types of plastics with different flow characteristics. And easy and precise weight selection mechanism ensures perfect testing. It’s vital for you to look for testers with a simple and intuitive method for adding and removing weight like sliding or lever-based system.
· The dye plays a very important role in melt index tester, so you need to look for a tester that offers perfect dimensional accuracy for reliable it is also. Accurate dimensions ensured that the flow rate measurements were consistent and comparable across various testers. The dye material must be resistant to wear and corrosion from molten plastic high-quality materials like hardened steel or tungsten carbide are perfect just as they maintain their integrity with time and use.
Additional features for efficiency
· A user-friendly interface with intuitive control simplifies the operation and reduces training time you need to look for MFI tester with clear menus and easy to understand control as it makes it easy for the operators to set up and run tests. Touch screen interface can improve the usability by providing more interactive and responsive control system. The testers with preset programs for different types of materials can save a lot of time and reduce the risk of user error
· And regular cleaning of the barrel piston and dye is really important for accurate measurements. You need to consider the design of melt index tester, as it allows for quick and easy assembly of components for different events.
· Safety is really important for any laboratory environment. You need to look for MFI tester that offers automatic shutdown features that activate if the tester overheats and can prevent accidents and equipment damage. Easily accessible emergency shutoff switches make it very easy for you to quickly stop the tester in case of any emergencies.
Integrating the testing into quality control process
You must know that regular testing ensures that the materials used in production meet the specific flow properties leading to consistent product quality.
Testing can detect different raw materials allowing for early identification and Correction of potential issues.
The testing helps you ensure that your products are aligned with the industrial standards and regulatory requirements reducing the risk of noncompliance
So above all you need to know that choosing the right melt flow index tester is important for obtaining accurate and reliable measurements in the plastics and polymer industry. By considering these key factors like temperature control weight system and dye design you can choose the tester that aligns with your specific requirements for instance additionally understanding the different types of testers and integrating them in your quality control process ensure consistent product quality and regulatory compliance. So, you just need to invest in good quality tester to improve the material testing capabilities and support your overall production efficiency.